Introduction:
The quest for an ideal denture base material has ever remained a challenge to the dental profession. Several materials have been tried with varying degrees of success & acceptance. The search, however, is still on to develop an ideal denture base material.
Denture bases are primarily made of metal or resins. Metal is not an ideal material since it is not aesthetic, has high co-efficient of thermal expansion and its fabrication is costly & technique sensitive. In contrast, resins have good aesthetic properties and they do not cause allergic reactions [1].
Since its introduction in 1937, Polymethylmethacrylate (PMMA) resin has maintained its superiority over the other denture base materials[2]. Although, many improvements have been made it sometimes fractures or crack in clinical use due to its low resistance to impact, flexural strength or fatigue failure [3].
Various approaches have been tried to improve the strength of (PMMA) resin, especially for its use in high stress areas in oral cavity. One such approach is to add a cross-linking agent such as polyethyeneglycol dimethacrylate. Others reinforce denture base polymer with fibers, metal wires or nets. Though these may increase the flexural and impact strength of denture base polymer, their use is limited because of the adverse effect on aesthetics [4].
The methods of incorporation of metal fillers into PMMA are difficult and the increase in flexural and tensile strength is not appreciable. Different workers have tried several non-metallic fillers such as nylon, rayon, glass, polyaramid, polyethylene, and carbon fibers as reinforcing agents. However there is no consensus regarding the exact improvement in enhancement of strength of PMMA.
Therefore, the present study was undertaken to accurately evaluate the increase in strength of PMMA by the incorporation of nylon, polyaramid, polyethylene, carbon fibers and glass (fibers & flakes).
Subjects and Methods:
In the present study, strength characteristics of PMMA and PMMA incorporating 6 types of non-metallic fillers were studied. Specimens of unfilled PMMA and those reinforced with glass fibers, glass flakes, carbon, nylon, polyaramid and ultra high modulus polyethylene fibers were prepared and designated as group A, B, C, D, E, F and G respectively. They were tested for tensile, compressive & izod impact strengths. These specimens were prepared using PMMA (Trevalon*).
Preparation of Samples:
a) Preparation of standardized stainless steel moulds:
To have all the test specimens of similar dimensions stainless steel moulds were prepared according to ISO standards(fig. 1).
 | Figure 1
 |
A stainless steel cylindrical (Diameter = 15mm, Length = 8mm) was prepared for testing compressive strength and a rectangular mould (Width = 6.5mm, Length = 10mm, Thickness = 3.3mm) was prepared for testing izod impact and tensile strength(fig. 2).
 | Figure 2
 |
b) Preparation of wax patterns:
i) For impact & tensile strength:
140 wax patterns (70 each for impact and tensile strength) were prepared by pouring molten wax in the stainless steel mould(fig. 3). Any defect after wax was hardened was corrected to get the accurate dimensions. The patterns were then removed from the mould.
ii) For compressive strength:
70 wax patterns (10 for each group) were prepared. Cast metal (nickel-chromium) ingots of uniform size were used to make the specimens. The impression of the metal ingots was made in silicon based impression material and filled with molten wax, defects if any was corrected. The wax patterns were then flasked and cured.
iii) Preparation of PMMA Test Specimens:
The wax patterns were flasked and dewaxing was done. A single coating of even thickness of separating medium was applied on each half of the flask using a hairbrush.
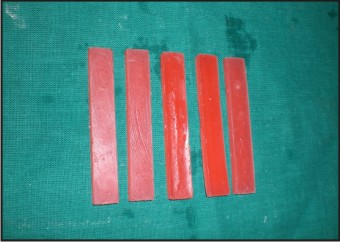 | Figure 3
 |
Acrylic resin powder and liquid were taken in the ratio of 2:1 by weight and were mixed in a porcelain-mixing jar with a lid. When the mix reached the dough stage it was packed in the moulds. After trial closure, the two halves of the flask were finally closed ensuring metal-to-metal contact. Polymerization was carried out by a long curing method employing a temperature of 74oC for 9hrs in an automatic thermostatically controlled curing unit.
The PMMA specimens were then removed from the flasks, finished to remove flash and any roughness present. These specimens were used as control and designated as Group A.
The procedure was repeated to obtain 30 PMMA specimens, ten each for testing tensile, izod impact & compressive strengths.
iv) Preparation of PMMA Reinforced Test Specimens:
Six types of non-metallic fillers (fibers & flakes) were used namely, Glass fibers, Glass flakes, Polyacrilononitrile (PAN) based high tensile type II carbon fibers, Nylon fibers, wholly aromatic poly para-phenylenderphalamide aramid fibers and Ultrahigh-modulus polyethylene (UHMPE) fibers.
Incorporation of fibers:
All the fibers were wrapped in aluminium foil and were cut into 5mm length with the help of sharp BP blade in order to have uniformity in length.
The amount of polyaramid, polyethylene, glass, nylon, carbon and glass flakes incorporated into the PMMA was 5 % by weight in each case. The powder and liquid were taken in the ratio of 2:1 by weight. Prior to mixing of the fibers the amount of powder equal to the weight of the non-metallic fillers was reduced, to ensure 5% concentration of the fibers in the mix.
Polymer & monomer were weighted individually in digital weighting machine and 5% of total weight fibres were incorporated. The fibers were thoroughly wetted with monomer for at least 5minutes prior to adding the polymer. The components were mixed thoroughly to disperse the fibers uniformly. Once the dough stage was reached, it was packed into the moulds and processing and finished in manner similar to the control group. In all 30 test specimens of PMMA reinforced with various types of fibers were obtained for each group and designated as:
Group B - PMMA + Glass fibres.
Group C - PMMA + Glass flakes.
Group D - PMMA + Carbon fibres.
Group E - PMMA + Nylon fibres.
Group F - PMMA + Poly Aramid fibres
Group G - PMMA + Polyethylene fibres.
Testing of specimens:
20 specimens from each group were selected at random and tested for tensile strength (Fig. 4) and compressive strength (Fig. 5) by Universal Testing Machine (Instron)*. Remaining 10 specimens were tested for izod impact strength (Fig. 6) using impact tester.
 | Figure 4
 |
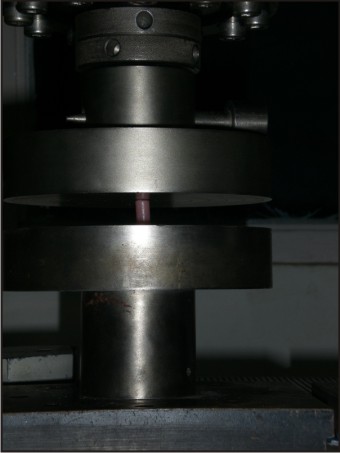 | Figure 5
 |
 | Figure 6
 |
The mean values for tensile, compressive & izod impact strength was calculated. These were recorded, studied, compared & statistically analyzed.
Statistical Analysis:
SPSS version 12.0 software carried the statistical analysis. Significance difference between groups was calculated by using ANOVA and unpaired‘t’ test and p<0.05 was taken as statistically significant.
Results:
(Table I) shows the values of mean ± standard deviation of each group for the tensile, compressive & impact strengths.
(Table II) shows significant difference among all groups at 0.01% & 0.05%.
 | Table 1 : Shows The Values Of Mean ± Standard Deviation Of Each Group For The Tensile, Compressive & Impact Strengths.
 |
 | Table II: Two Way Repeated Measure Anova For Statistical Significance Between Study Groups At 0.01% & 0.05%.
 |
Results indicated that the reinforcement of PMMA with fillers resulted in significant increase in tensile & impact strengths and decrease in compressive strengths respectively when compared to unfilled PMMA. When compared to the control group, experimental groups did not show statistically significant difference in impact strength except for group G & F.
Discussion:
Charles Goodyear developed the art of vulcanizing rubber in 1839. One early use of this material was for making denture bases. Vernonite was the first of the acrylic resin compounds formulated for dentistry to be introduced in United States and was perhaps the first application of the monomer-polymer principle anywhere [5].
The Academy of Denture Prosthetics in 1967 gave guidelines for the denture base materials to be used. Physiological compatibility was judged the most important factor and cost to be least important for selection of a denture base material [6].
Acrylic resins have been used extensively for the fabrication of denture bases because they provide large number of advantages than any other material. However, one of the major drawbacks to use acrylic resin as denture base material is its susceptibility to fracture. The PMMA-denture base is far from being a satisfactory denture material in fulfilling the mechanical requirements of prostheses [7].
Acrylic denture base resins are available in two forms:
Gel or plastic cakes; with the gel or plastic cake, the monomer & polymer have been premixed & packaged as soft, rubbery, one-unit cakes ready for immediate use.
Powder-liquid; the powder-liquid is more common. The liquid is mixed with the powder, the monomer plasticizes the polymer to a dough stage, which is packed into the mold prior to polymerization of the monomer. The resulting denture base is composed of solid, homogenous resin [8].
Beyli[9] said that deformation and or movement of the denture during function will affect both supporting tissues and denture base itself. Maxillary dentures are subjected to bending deformation, with tensile stresses occurring at the labial aspect and lingually to the incisors, then onto the polished surfaces. Compressive stresses occur towards the tissue surface, with greater values beneath the teeth and on the ridge than those toward the palate.
Johnston[10] concluded that the fractures in dentures result from two different types of forces viz. impact and flexural fatigue. While impact may occur when denture is dropped, flexural due repeated flexing from chewing ultimately fatigues the dentures in the mouth.
Stress concentration in the material may be present in the unloaded state when thermal changes have occurred. Differential thermal contraction between an inclusion and the denture material or between the surface and the interior of the material itself produces residual forces due to the local restriction of the shrinkage of the polymer. The residual stresses reveal themselves as crack formation[11].
The intrinsic strength of the material is affected by the composition, which depends partly on the curing technique used. It is the amount of the residual monomer remaining after curing[12].
The inclusion of the metal strengtheners in the form of wires, meshes, plates usually resulted in the development of plane of coverage between the acrylic & the reinforcement because of greater thermal contraction of the metal, which could lead to early failure of the prosthesis[13].
Reinforcement of dental resin with short or long fibers has been described in the literature for nearly half a century now. Several different types of fibers have been used, with varying results but fiber reinforcement has never been adapted to routine clinical practice. Effective fiber reinforcement is dependent on many variables, including the type of fibers in the matrix, the modulus and distribution of the fibers, fiber length, orientation, forms, and interfacial bond.
Orthopedic acrylic resin-based bone cements have successfully been reinforced with glass, carbon, and aramid fibers. In periodontics, glass & polyethylene have been tested as additives to BIS-GMA resin for temporary splints to immobilize teeth. In orthodontics, the use of aramid fibers has been studied useful in reinforcing orthodontic appliances. In prosthodontics, fibers have been used to improve the fracture resistance or moduli of elasticity of polymer materials.
In the present study, five percent concentration of 5mm length of glass, carbon, nylon, polyaramid, UHMPE fibers were used to reinforce the PMMA heat cure denture base resin. The 5% concentration of fibers produced dry, friable dough which was difficult to pack at the recommended powder-liquid ratio of 2.5:1 by weight, so to avoid this 2:1 ratio of the mix was taken for proper wetting and mixing of the fibers.
On comparing tensile strength of the study groups, PMMA reinforced with Ultra High Modulus Poly Ethylene (UHMPE) showed maximum values and control group minimum values respectively. Therefore it is suggested that we choose such fillers for the reinforcement of acrylic resin in areas where there is maximum stress concentration. (Ex: in case of maxillary labial notch to provide relief for labial frenum.)
The control group exhibited higher compressive strength values than all the experimental groups suggesting that the reinforcement of PMMA with different types of fibers resulted in decrease of its compressive strength.
The impact strength when compared showed the maximum value for group G (PMMA + UHMP) i.e. 0.575 J/m2, group E 0.284 J/m2 having minimum value. The fibers prevent the propagation of the cracks as a result of higher concentration of stresses.
In case of compressive strength there was statistical difference in between all the groups but in the case of izod impact strength statistical difference was found only in group F & G. The mode of failure is when the material is stressed past its limits. The mode of failure for glass fibers is due to the splintering (breakage), whereas in case of the polyethylene fiber is due to their bending i.e they don’t fracture. Nylon & aramid fibers proved difficult, because during packing of reinforced acrylic resin, some fibers spread out laterally in the mold. This could be observed by opening the flask after the trail closure. In order to overcome this problem, through kneading of the monomer-fibers-polymer was carried out prior to packing.
Results of the present study indicate that reinforcement of acrylic resin by ultra high-modulus polyethylene, polyaramid, carbon & nylon fibers & glass (fibers & flakes) especially UHMPE results in significant increase in tensile & impact strength of PMMA. Areas in complete denture where there is likelihood of fracture (eg. upper complete & lower natural teeth) selective reinforcement of maxillary denture is advisable to prevent or minimize the chances of fracture as a result of stress concentration.
PMMA, which is most extensively used as a denture base material, does not fulfill all the desirable properties especially those regarding the strength & polymerization shrinkage. In foreseeable future another material, which can overcome the shortcoming of acrylic resin, could be developed, in view of the ongoing research.
References:
1. Kanie T., Arikawa H., Fujii K., Ban S. (2004) Flexural properties of denture base polymers reinforced with glass cloth-urethane polymer composite. Dental Materials 2004; 20: 709-716.
2. Aydin, Yilmaz, Caglar(2002) Effect of glass fiber Reinforcement on the flexural strength of different denture base resins. Quintessence International (2002) 33,457-463.
3. Kanie T., Fujii, Arikawa H., Inoue K. (2000) Flexural properties & impact strength of denture base polymer reinforced with woven glass fibers. Dental Materials 2000; 16: 150-158.
4. Franklin P, Wood DJ, Bubb NL (2005) Reinforcement of poly (methyl methacrylate) denture base with glass flake. Dent Mater 2005; 21: 365-70.
5. Bowman A. J.,Manley T. R. (1984) The elimination of breakage in upper dentures by reinforcement with carbon fiber. Br. Dent. J. 1984; 156: 87-89.
6. Academy of Denture Prosthetic (1968) Final report of the workshop on clinical requirements of ideal denture base material. J Prosthet Dent 1968; 20: 101- 105.
7. Solnit G. S. (1991) The effect of methyl methacrylate reinforcement with silane-treated glass fibers. J Prosthet Dent 1991; 66: 310-4.
8. Mullarky R.H. (1985) Aramid fiber reinforcement of acrylic appliance. JCO 1985; XIX (9); 655-85.
9. Beyli M. S., Von Fraunhofer J. A. (1981) An analysis of causes of fracture of acrylic resin dentures. J Prosthet Dent 1981; 46 (3): 238-41.
10. Johnston E. P., Nicholls J. I., Smith D. E. (1981) Flexural fatigue of 10 commonly used denture base resins. J Prosthet Dent 1981; 46: 478-83.
11. Anusavice (2003) Phillips Science of dental materials. Eleventh Edition.
12. Foo H., Lindquist T. J., et al. Effect of polyaramid fiber reinforcement on the strength of 3 denture base polymethylmethacrylate resins. J Prosthodont 2001; 10: 148-53.
13. Randall A. E, Cleary, Jamesnd. (1995).Method of manufacturing orthodontic appliance having reinforcing fiber preform Us Patent 5445770 1995. 29.
|